Raw Materials
Semolerie Giuseppe Sacco & Figli is well-known today on the market for the quality of its products marketed as durum wheat semolina, durum wheat flour and diced durum wheat bran.
Semolerie Giuseppe Sacco & Figli not only interacts with its customers on internal and external levels, but also seeks to establish loyal relationships with its suppliers, selecting only the best raw materials on the market and building relationships based on trust and mutual esteem.
Delegating responsibility to employees, partners and suppliers seeks at all levels to achieve the best results in terms of product quality and competitiveness, in compliance with principles such as environmental protection and safety.
Cleaning
After storage in silos, the wheat is mixed and transported in relation to the kind of processing to be carried out for cleaning: bucket elevators carry the grain to the upper floors, which then falls through pipes and enters a magnet that extracts any metal bodies.
The grain then passes into the “Vega” vibro-separator with sieves (to separate straw and soil), the combiners and the stone picker.
The mixture processed in this way is sent to an air-recirculation ventilated sieve which conveys the product into the Sortex – an optical sorter that eliminates any impurities such as black grains, spotting or black wheat germs. The grain is then conveyed into an intensive wheat bath with an automatic centralized system that regulates the flow of water needed to wet the grain in relation to its humidity and quantity.
Conditioning
The conditioned grain then moves on to the reinforced concrete conditioning silos and, after resting for about 10 hours, undergoes a second cleaning process.
Machines equipped with grinding wheels then husk the wheat: all external parts of the kernels are eliminated before being milled; this is an extremely important step as regards the elimination of chemical and biological impurities.
The entire cleaning and conditioning process works alongside a suction system, connected to all the machines, to ensure cleanliness and avoid dust-powder deposits that other cause contamination and even fires.
Milling
Once the cleaning and conditioning process is completed, the wheat passes through another magnet mounted in the lower head of another elevator; it is weighed and then sent to the milling department, which has a series of machines capable of separating bran from the kernels.
The milling involves the following stages:
MILLS
SIFTERS
PURIFIERS
MILLS
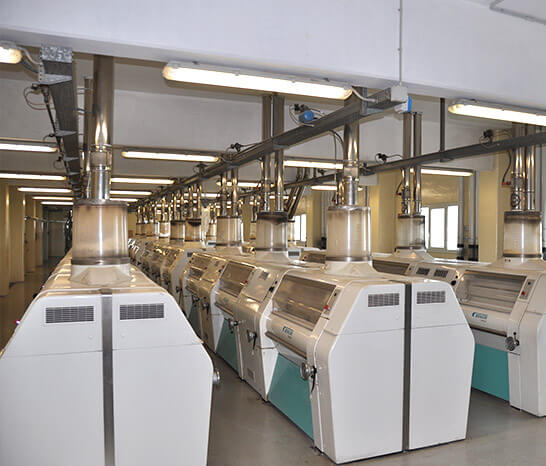
SIFTERS

PURIFIERS
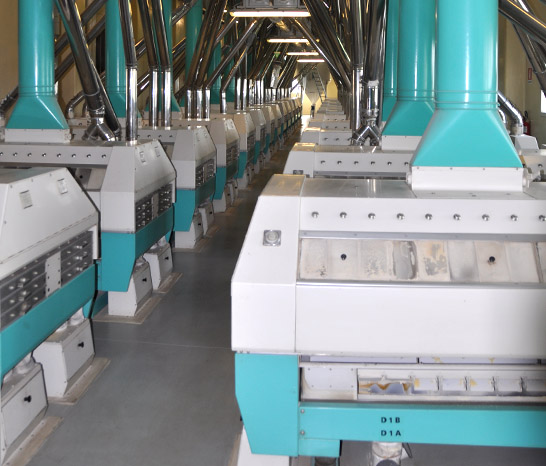
Storage
The entire production process is based on stainless steel pipes and air-operated ducts. This system means that the grain reaches the upper floors thanks to a high pressure fan that sucks and decants the product from the pneumatic lines.
After cleaning, conditioning and milling, the wheat is divided into finished products: the flour passes through an automatic scale that weighs the product before conveying it to storage silos. Here, it is loaded on to vehicles suitable for transporting flour for human consumption thanks to an automatic, computerised system that controls the machines in relation to the load to be handled.
Semolerie Giuseppe Sacco & Figli srl.

AddressS.S. 17 km 327,00
71036 Lucera FG

Office Hours09:00 AM – 1:00 PM3:00 PM – 7:00 PM

Phone +39 0881/520788 +39 0881/520789+39 0881/549209
Fax + 39 0881/549195

Info info@semoleriesacco.it
PEC semolsacco@pec.it